The superstructure is built off-site for either case however with different structural strength.
Structural load requirements:
- Wind: 150 mph (3-sec gust)
- Seismic Design Category: E
- Live Load, LL: 100 psf main floor, 60 psf roof deck
- Snow Load, SL: 60 psf
- Dead Load, DL: 15 psf + Water tanks
To build an On-Site superstructure in a factory one needs:
- Columns: HSS 6”x3”x1/4”
- Roof Beams: HSS 6”x3”x1/4”
- Existing Trailer Reinforcement (see figure 2): 2’-0” long 11-5/8” x 3/16” A36 steel plates welded 2” @ 6” centered below columns (1’-0” long at ends) see figure 1 below:
These are based on welded connections.
To build a mobile superstructure in a factory:
For trailer being used to transport complete structure/building,
- reinforce the main trailer beams the entire length with 11-5/8” x 3/16” A36 steel plates welded 2” @ 12” spacing minimum on each side of the beam such as shown on figure 1 below. This configuration will still allow the proposed pier supports to attach to the beams.
- The tongue and trailer beam above tongue will have to be replaced with a custom built one in order to support the loads during transit. Structural engineer suggest using HSS 10”x4”x3/8” A500 Gr. C steel tube, or similar strength beams.
- The max total weight of 43,200 lbs for the structure, assuming no live loads, empty water tanks, and 15 psf dead load on floor and roof. Max dynamic reactions induced while in-transit are expected to be double the loads shown of stationary.
- In-Transit Impact: 2G (2 x DLtotal) Transported to site on trailer and existing 5 axles and then set on piers. Expect around 10,000 lbs on tongue hitch, and 3,660 lbs max per side of an axle of one of the 5 axles of the existing trailer, or 7,320 lb per axle.
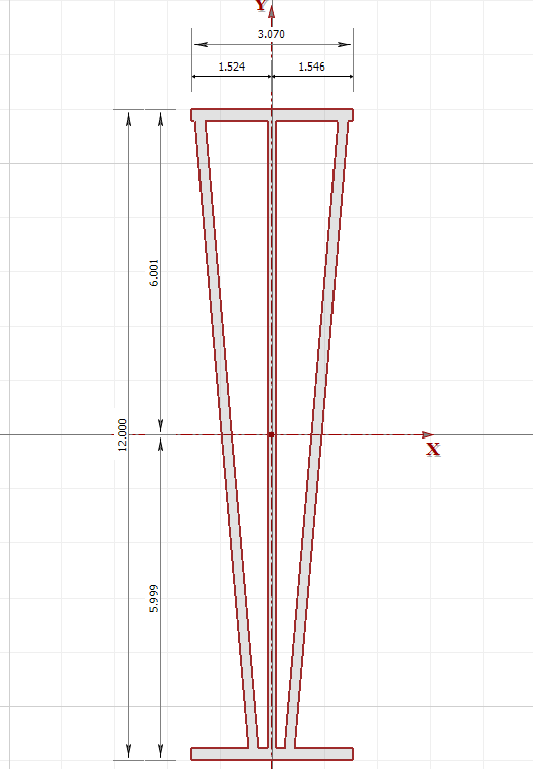
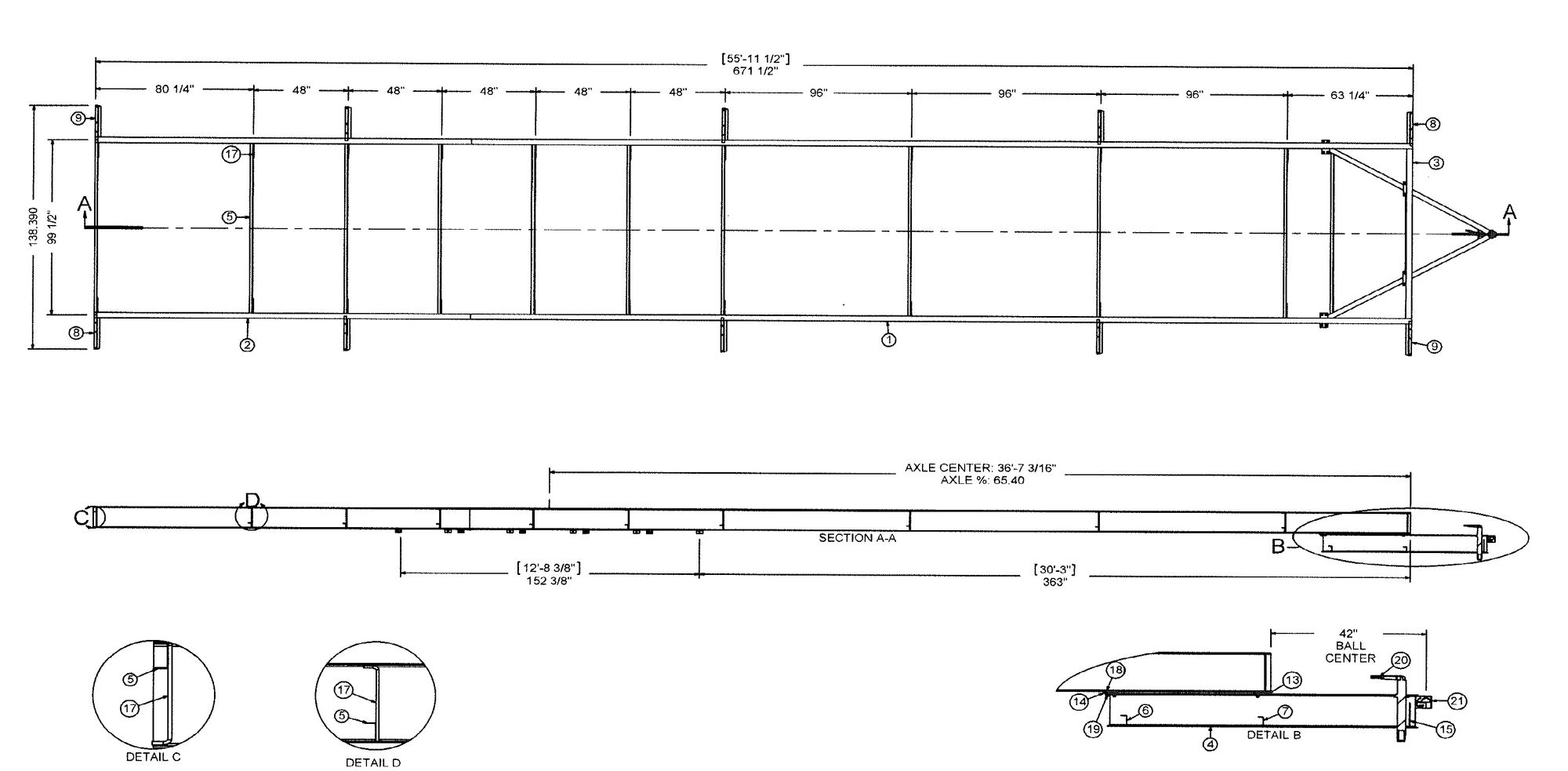
Light Gauge Metal Framing is same for both structures (see figure 3):
- Floor Joists: 1200S250-68 (12” x 2.5” x 14ga) @ 24” o.c.
- Roof Joists: 600S250-54 (6” x 2.5” x 16ga) @ 24” o.c.
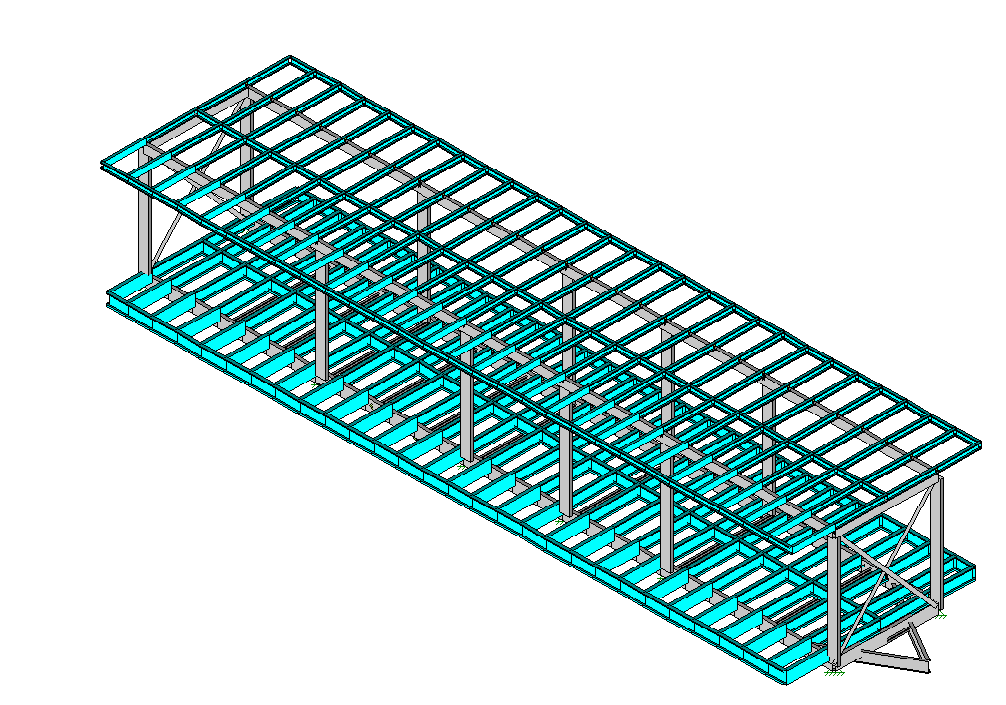
Pier Spacing and Reactions:
Based on the structure being installed on site and experiencing max forces, we determined that piers shall be placed under each column and spaced no more than 10 feet on center. Approximately 9 piers per side, 18 total.
Maximum reactions, including lateral forces are expected to be 17,000 lbs vertical, 3,200 lbs horizontal, and 1,600 lbs uplift.
Angel Landings system provides a structural design that is easy to assemble and requires minimal leg work to build. We took a trailer chassis from a reputable manufacturer and reinforced it to handle addition vertical loads. To create the super structure we added a moment frame to a trailer chassis. By now you must be asking why would I build on top of the chassis? It is quite simple why, first it qualifies for US Federal HUD approval vs local state city level. Second it makes it easy to assemble the super structure off-site and ship it on wheels. Chassis with superstructure simplifies the construction logistic and cost associated with it.
The light frame steel structure is easy to assemble either on site or off-site and requires no scaffolding or heavy lifting equipment.
The chassis is built with a tongue hitch so that it can be easily shipped by using a tractor trailer truck.
HUD requirements:
To qualify for federal approval one must use DAPIA (manufactured housing and HUD) a federal inspection agency. If the state jurisdiction prohibits use of Federal code, then one needs to file and inspection under local state modular building code or IBC.
A local builder should verify with a local engineer to see if structural calculation meet the minimum load requirements for local wind loads, seismic, and soil strength. Also, to file under federal agency DAPIA one would need a signed and sealed drawing from a US registerer engineer.
Builder installing the structure unit onto above ground piers footing would need to attach the piers after the structure is delivered to its location. However, if the footing is installed below ground level, then the footing needs to be professionally installed by a licensed foundation contractor for trailer buildings/homes.
Additional metal accessories are:
- Retractable steps can adjust up to 44 inches. There are good for offsite living where retractable stairs can prevent unwanted guest into ones unit. Please note retractable steps are not IBC compliant and may be unsafe for young kids. To learn more about retractable steps and details please download the metal frame package.
- For exterior finish we recommend Vesta metal panel system. These are corrosion resistant, built strong and have quality imprinted wood grain textures. They are easy to install.
- We recommend using a standard metal wire railing that can be assembled on site easily.
- Painted corrosion resistant steel angle are to be used to frame the EPDM roofing and roof insulation.
Specs:
- Trailer frame by Lippert Components Inc.
- Exterior wood decking by Geolam
- Exterior metal panels and finishes by Qualityedge – Vesta
- Foldable steps by Solid Steps from Lippert Components
- Stair for Roof top access by Erectastep